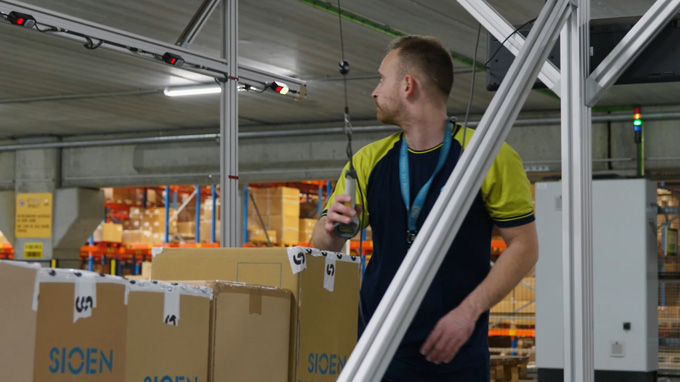
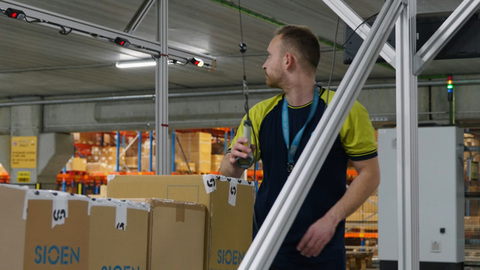
Pick-by-Light accélère la logistique manuelle de plus de 60 %.
Comment un système de guidage par la lumière accélère considérablement les processus de tri et de préparation des commandes et réduit drastiquement les taux d'erreur.
Sioen Apparel est un spécialiste des textiles techniques et des vêtements de protection. Il développe, produit et vend des fils, des tissus, des non-tissés, des textiles et des vêtements pour diverses applications dans le monde entier. Afin d'optimiser les processus d'entrée et de sortie dans son centre de distribution de Mouscron, en Belgique, Sioen a mis en place un système de gestion d'entrepôt haute performance en combinaison avec une solution pick-to-light basée sur la série PTL110 de Banner Engineering, partenaire de Turck pour les capteurs optiques, et les modules d'E/S TBEN IP67 de Turck. En utilisant les modules d'affichage en cascade avec bouton tactile et capteur optique en option, les taux d'erreur ont été considérablement réduits et les processus de tri et de prélèvement nettement accélérés.
Toute personne qui travaille dans des environnements difficiles et potentiellement dangereux a besoin de vêtements de protection de qualité qui la protègent contre les blessures ou les accidents. L'entreprise belge Sioen est spécialisée dans les textiles techniques et les vêtements de travail de protection. Elle produit plus de trois millions de vêtements de protection sur 22 sites répartis dans 20 pays. Sur le site de Mouscron, l'entreprise familiale exploite un grand centre d'expédition et de distribution en plus de quatre usines de production. Les vêtements produits dans le monde entier y sont traités, stockés et préparés afin d'être expédiés aux clients rapidement et efficacement.
Auparavant, les processus d'entrée et de sortie étaient en grande partie réalisés manuellement. Après la livraison, les palettes étaient transportées jusqu'à un collaborateur qui scannait les cartons individuellement et les plaçait sur les positions définies des palettes. Il fallait environ cinq à quatre heures ou cinq collaborateurs pour traiter un camion.
Un collaborateur de la zone de sortie recevait une liste de prélèvement pour chaque client et parcourait les magasins pour récupérer les marchandises. "Ce n'était évidemment pas une manière efficace de travailler", se souvient Filiep Vanwymelbeke, responsable de la logistique chez Sioen Apparel. "Nous avons donc cherché un système capable de relever les défis de la logistique tant entrante que sortante." Nous avons finalement mis en œuvre un puissant système de gestion d'entrepôt (WMS) pour résoudre ce problème, en combinaison avec une solution pick-to-light sans erreur basée sur la série PTL110 de Banner Engineering, partenaire de Turck pour les capteurs optiques.
Inbound : pick-to-light comme meneur de jeu
Dans la zone des marchandises entrantes (inbound), les employés soulèvent les cartons des palettes pour les placer sur un tapis roulant. Un scanner capture automatiquement les étiquettes sur les cartons au fur et à mesure de leur passage. En fonction de l'étiquette, ils sont ensuite dirigés vers l'un des six tapis roulants. Une fois qu'un collaborateur situé à l'extrémité du tapis roulant a scanné le carton livré, le WMS indique immédiatement, via le système pick-to-light, sur quelle palette il doit être placé. Le collaborateur place le carton sur la palette appropriée et confirme l'action par le biais du bouton tactile du dispositif PTL110 situé au-dessus de la palette.
Le système pick-to-light fournit plusieurs états de signal. Lorsque, par exemple, la palette est complète et peut être retirée, la LED du PTL110 s'allume en bleu.
Outbound : consolidation fiable des commandes
Deux flux de marchandises convergent sur le convoyeur de sortie : Des cartons avec un contenu standard et des cartons avec un mélange de différentes marchandises. Le collaborateur scanne le carton, après quoi le WMS détermine la palette sur laquelle il doit être placé. Les PTL110 indiquent l'emplacement correct de la palette au moyen de simples signaux de couleur. "Nous sommes très satisfaits de cette méthode de travail", déclare M. Vanwymelbeke. "Nous envisageons de doubler le nombre d'appareils PTL110 dans la zone de sortie afin de servir encore plus de clients et de transporteurs en même temps."
Le module d'E/S multi-protocole assure un fonctionnement fiable
La communication des dispositifs PTL110 avec le WMS est cruciale pour le fonctionnement optimal de la solution. Tous les appareils PTL110 sont connectés à cet effet via les modules d'E/S multiprotocoles TBEN-S de Turck. Les modules IP67 robustes peuvent être montés directement sur la ligne de convoyage sans armoire de commande et sont équipés en standard du logiciel de contrôle logique de terrain ARGEE basé sur le Web.
La communication avec le WMS peut être facilement configurée à l'aide de PickIQ. Le personnel informatique du client n'a pas besoin de connaissances particulières en matière de logiciels d'automatisation pour cela.
Taux d'erreur réduit à zéro
La polyvalence des dispositifs PTL110 est démontrée par leur application dans les systèmes entrants et sortants. Ils se distinguent par leur temps de réponse rapide et leurs options d'installation flexibles, qui permettent de personnaliser et d'étendre facilement le système. Les connecteurs M12 permettent une installation rapide et sûre de plusieurs dispositifs.
"Le taux d'erreur à l'arrivée est tombé à pratiquement zéro", note Vanwymelbeke. "Alors qu'il fallait auparavant jusqu'à cinq heures à cinq coworkers pour traiter un camion, il est désormais traité par trois coworkers en deux à trois heures. Cela correspond à un gain de temps allant jusqu'à 16 heures par camion et par jour. De cette manière, nous pouvons utiliser nos employés pour d'autres tâches."
Informations complémentaires
- Automobile
- Flexibilité modulaire et sécurité dans la production de filtres
- Un câble avec surveillance de courant intégrée empêche l'arrêt intempestif du système de transport
- Les coupleurs inductifs assurent une alimentation précise du matériau
- Gestion des assemblages avec une connexion MES directe
- Détection des corps dans la production automobile
- Détection fiable des dérapages dans la production automobile
- Préparation de commandes JIS sans erreur pour les pare-chocs
- Un capteur laser détecte les cylindres brillants dans la production de batteries
- Le mode bus RFID garantit la qualité des batteries au lithium-ion
- Mesure de niveau dans une ligne d'enduction par trempage
- Contrôle du niveau dans le système de lubrification centrale
- Assurance qualité sur le robot de collage
- Le capteur d'angle d'inclinaison accélère l'alignement de la plate-forme
- Contrôle des Moteurs avec Condition Monitoring
- Module hybride IP67 Processus de traitement des signaux de sécurité
- Surveillance décentralisée des stations de refroidissement
- Cellules de soudage robotisées mises en réseau par Ethernet
- Surveillance du circuit de refroidissement des pinces à souder
- Contrôle du débit dans les laveurs de tambours
- Mesure d'épaisseur de tôle
- Condition Monitoring des moteurs
- Contrôle de niveau basé sur le cloud
- Atelier de presse – Identification d'outils
- Carrosserie – Détection des écrous à souder
- Atelier de peinture – Identification de skids
- Montage final – Montage robotisé
- Mécanique – Vérification sans contact
- Protection de zone pour les cellules robotisées
- Détection au niveau des articles avec la RFID UHF
- Fourniture de réfrigérant lubrifiant dans les machines-outils
- Contrôle de la pression hydraulique dans les usines de pressage
- Mesure de la pression de processus sur les élévateurs à ciseaux
- Inspection des becs sur des robots de soudure
- Chargement manuel dans une cellule de soudage
- Détection de pièces noires sur des panneaux de porte noirs
- Détection de verre transparent sur un toit vitré
- Inspection à longue portée dans le secteur de l'assemblage automobile
- Détection de rondelles de caoutchouc sur un bloc moteur
- Détection du positionnement des pièces dans un bloc moteur
- Détection de véhicules électriques aux bornes de recharge
- Détection de voitures dans un car-wash en libre-service
- SUCCESS STORIES
- RFID Solution for Data Acquisition in Stator Production
- Modular Plant for Flexible and Efficient Production
- Un capteur laser détecte les pare-chocs noirs dans une cellule d'assemblage
- Technologie de sécurité décentralisée pour une production modulaire
- Système de transport modulaire
- Modules RFID et E/S pour des changements d'outils en toute sécurité
- La technologie RFID pour guider un chariot autoguidé dans la production de suspensions
- Production de silencieux filaires IO-Link
- Identification des porte-pièces dans la production de systèmes de ventilation arrière
- Détection d'écrous à souder
- Traçabilité RFID
- Technologie RFID dans la production de moteurs
- Production de pare-chocs avec système d'identification
- Solutions pour ateliers de peinture
- Capteurs de soudage et d'assemblage
- Capteurs d'angle pour systèmes d'assemblage
- Identification d'outils
- Système d'aide au choix pour la production de modules de pilotage
- Identification RFID des buses d'injection
- La technologie RFID dans l'atelier de carrosserie
- IO-Link facilite la production d'engrenages différentiels
- Inspection d'orientation de couches
- Chimie
- Le système d'E/S excom permet une liquéfaction sûre de l'hydrogène
- Automatisation décentralisée dans les zones Ex
- Contrôle RFID des raccords de tubes dans la zone Ex
- Connexion du signal Ethernet dans la salle I&C
- Automatisation des skids modulaires par Ethernet
- Isolation Ex dans les usines de traitement modulaires
- Détection d'écouvillons
- Télésurveillance des niveaux de cuves avec le DX70
- Systèmes d'E/S déportés pour le traitement de signaux
- Connexion aisée des équipements de terrain
- Traitement des signaux avec un système d'E/S dans l'armoire de commande
- Séparation des signaux avec une technologie d'interface dans une armoire de commande
- Identification de raccords de tuyaux
- Surveillance efficace d'armoires sur le terrain
- Surveillance d'actionneurs quart de tour
- Planification et assemblage de solutions système
- Success Stories
- Moniteur d'armoire de commande pour la transmission des données d'état
- Efficient Cooling of Industrial Furnaces with Turck's FS+ Flow Sensors
- Gain d'espace dans les salles I&C grâce au système d'E/S excom
- Technologie RFID pour les zones 2 et 22
- Contrôle de test efficace
- Communications de terrain intrinsèquement sûres
- Développement d'un système de contrôle des processus en partenariat
- Système d'E/S déporté pour zones dangereuses
- Double retour d'information sur la position des vannes
- La flexibilité offerte par un bus de terrain
- Gestion des actifs avec un système d'E/S déporté
- Positionnement correct avec la technologie RFID dans la production de carbure
- Conversion rapide dans un espace restreint
- Energie
- Un système RFID identifie les porteurs de cellules solaires
- Système d'E/S décentralisé pour les zones dangereuses des stations de ravitaillement en carburant H2
- Decentralized I/O Solution in Ex Zone for H2-Fueling Station
- Le module E/S facilite l'installation et l'utilisation mobile du banc d'essai pour piles à combustible
- Positionnement du rotor sur les éoliennes
- Systèmes d'E/S IP67 dans l'industrie houillère
- RFID UHF pour l'identification de disjoncteurs
- Système d'E/S déporté dans une installation de biogaz
- Agro-alimentaire
- Le suivi RFID réduit le gaspillage alimentaire dans la production de crème glacée
- Contrôle de la hauteur de la pâte pour une mesure précise
- Un capteur de Condition Monitoring pour automatiser le contrôle du climat
- Condition Monitoring des armoires de commandes
- Condition Monitoring dans les entrepôts
- Contrôle de l'épaisseur de pâte dans des lamineuses
- Détection du bord avant d'une barquette en plastique
- Identification de conteneurs alimentaires
- Vérification de récipients
- Vérification de l'exactitude de la date et du code de lot
- Détection de la position d'une vanne
- Détection de coudes de tuyaux
- Identification de moules à pralines
- Lecture de codes à barres dans un poste de dépalettisation
- Success Stories
- Maintenance des générateurs de vapeur basée sur le cloud
- Le support RFID permet le suivi et la traçabilité dans la production alimentaire
- Détection de position linéaire fiable en zone Ex 22
- Modules de contrôle décentralisés dans les entrepôts frigorifiques
- Track &Trace dans le secteur de la production de viande grâce à la RFID
- Codeur sans contact pour la production de pommes de terre
- Technologie UHF-RFID dans un centre de distribution alimentaire
- La technologie RFID pour la production de pralines
- E/S distribuées pour l'équipement de production alimentaire
- Système d'E/S déporté pour les distilleries
- RFID et autoclaves
- Transparence dans la fabrication du chocolat
- Systèmes d'alimentation IP67 pour convoyeurs
- Identification dans l'entreposage de produits alimentaires
- Détection de petits pains réfrigérés sur un convoyeur multivoie
- Vérification fiable de l'orientation des bouchons dans des espaces aseptisés
- Détection de bouteilles transparentes renversées sur un dépalettiseur
- Détection de bouteilles en plastique transparent
- Inspection d'étiquettes d'emballages alimentaires surgelés
- Accumulation de bouteilles en file sur une aligneuse simple
- Logistics
- UHF RFID Tunnel for Goods Identification on Conveyor Belts
- Surveillance des circuits de refroidissement et de lubrification des machines CNC
- Prévenir les bourrages de colis dans le centre logistique
- Contrôle de la hauteur et surveillance spatiale 3D sur les chariots élévateurs autonomes
- Decentralized Control of Conveyor Modules
- Suivi des grands sacs avec la RFID
- Détection de la distance dans les grues à conteneurs
- Contrôle d'accès aux zones protégées
- Muting décentralisé des équipements de protection électro-sensible
- Blocs d'E/S Modules de contrôle du convoyeur à rouleaux
- Contrôle des conteneurs
- Détection rapide des étiquettes aux portes des entrepôts
- Détection au niveau de l'article avec la RFID UHF
- Maintenance préventive sur les bandes transporteuses
- Détection des conteneurs de transport
- Détection de niveau dans les récipients
- Identification des enceintes cryogéniques
- Identification des conteneurs mobiles à l'aide d'appareils portatifs
- Identification de conteneurs alimentaires
- Niveau 1 - Identification des pare-chocs
- Surveillance de l'état des locaux de stockage
- Protection contre les collisions sur les Reach Stackers
- Success Stories
- Efficient Solution for the Digitalization of Conveyor Technology
- Logistique : la technologie RFID réduit le taux d'erreurs de 99 %
- Retour sur investissement après trois erreurs de livraison évitées
- Contrôle fiable des AGV grâce à une solution complète basée sur des capteurs
- Suivi durable des RTI grâce à la RFID
- Solution RFID pour la logistique des matériaux à l’épreuve des erreurs
- RFID with HF Bus Mode Eases Seed Storage
- Pick-by-Light accélère la logistique manuelle de plus de 60 %.
- La solution Pick-by-Light facilite les processus d'assemblage
- La RFID permet la mise en place d'un magasin sans personnel sur un grand chantier de construction
- Les modules d'E/S et de sécurité augmentent le débit de l'intralogistique
- Suivi des expéditions de matières premières
- Solution de suivi basée sur la RFID pour minimiser les erreurs de chargement
- Suivi par RFID des matériaux entrants et sortants
- Solution RFID UHF décentralisée
- Encodeur sans contact dans la production de pommes de terre
- L’automate IP67 contrôle les quais de déchargement de chambres froides
- Contrôle de la vitesse par capteur radar QT50
- Alimentations IP67 pour les convoyeurs
- Système de transport modulaire
- Solution RFID pour entrepôts
- La RFID guide l'AGV dans la production de suspensions
- La RFID identifie les produits pharmaceutiques
- Technologie UHF-RFID dans un centre de distribution alimentaire
- Aide au stationnement autonome pour les camions
- Equipement Mobile
- Détection d'animaux et d'objets sur la moissonneuse-batteuse
- Un capteur de Condition Monitoring pour automatiser le contrôle du climat
- Surveillance de l'occupation d'un quai de chargement
- Surveillance sans fil de roues de train
- Compensation automatique de la pente
- Lignes de distribution pour pulvérisateurs agricoles
- Indication de l'état des reach stackers à l'aide de voyants lumineux intenses
- Mesure d'angle sur un pulvérisateur agricole
- Surveillance du sens de déplacement du matériau sur une moissonneuse-batteuse
- Détermination du positionnement angulaire de la flèche
- Véhicules dans une zone de chargement
- Signalisation sans fil pour chariot élévateur
- Éclairage de compartiments de rangement des équipements sur des véhicules de pompiers
- Mesure de l'inclinaison sur deux axes pour une moissonneuse-batteuse
- Protection contre la collision sur des reach stackers
- Success Stories
- Solution RFID avec chariots élévateurs intelligents en production automatique
- Maintenance à distance en toute sécurité des pompes d'irrigation et de drainage
- Contrôle d'accès avec système RFID
- Récolte sélective des asperges avec un robot autonome
- Mesure de la position avec la technologie RFID et un codeur
- Contrôle de la vitesse avec le capteur radar QT50
- La technologie RFID pour guider un chariot automatisé dans la production de suspensions
- Modules d'E/S sur un super yacht
- Codeur inusable sur une drague porteuse
- Système d'E/S pour éliminer la poussière
- Refroidissement d'armoire de commandes
- Connectique à raccord rapide
- Solutions d'automatisation pour le froid extrême
- Système d'E/S déporté pour des grues
- Elévation de métaux lourds et robustes
- Mise en place des montagnes russes
- Solutions pour machines mobiles
- Capteurs de position linéaires inductifs équipés d'une interface IO-Link
- Inclinomètres sur les camions des pompiers
- Maintenance prédictive des pièces des machines dans une infrastructure de transport du charbon d'un port
- Détection des nacelles élévatrices par un capteur d'angle
- Pétrole et Gaz
- Emballage
- Vérification décentralisée des emballages RFID
- Identification de cartouches d'impression couleur
- Fonctionnement fiable des machines
- Surveillance des bouchons sur des lignes de remplissage
- Surveillance des processus de changement de produits
- Identification de bouteilles de test
- Détection de la notice d'information dans une boîte
- Surveillance du niveau de remplissage de café moulu
- Détection du niveau de remplissage des récipients
- Calcul des dimensions des boîtes en carton
- Détection de bacs de transport
- Success Stories
- Détection de barquettes transparentes
- Vérification de la présence d'étiquettes correctes
- Détection de boîtes de différentes tailles sur un convoyeur
- Contrôle des codes à barres 2D à haute vitesse
- Détection d'emballages réfléchissants multicolores
- Mesure de diamètre d'un rouleau de film en plastique
- Positionnement de tubes à l'aide d'un repère
- Solutions pour ensacheuse verticale
- Pharma
- Suivi des échantillons du début à la fin grâce à la RFID
- Contrôle RFID des raccords de tubes dans la zone Ex
- Vérification décentralisée des emballages RFID pour les produits pharmaceutiques
- Automatiser les skids modulaires
- Comptage de comprimés à haute vitesse avec un amplificateur fibre
- Skids pharmaceutiques avec technologie E/S décentralisée
- Isolation Ex dans les usines de traitement modulaires
- Contrôle décentralisé des interfaces de vannes
- Détection de liquide dans des poches pour perfusion
- Surveillance d'actionneurs quart de tour
- Détection de coudes de tuyaux
- Systèmes d'E/S déportés
- Surveillance de niveau de liquide dans une grande cuve
- Planification et construction de superskids
- Connexion aisée des équipements de terrain
- Identification de récipients cryogéniques
- Identification de contenants en mouvement
- Identification de contenants en mouvement à l'aide de terminaux portables
- Identification de raccords de tuyaux pour des précurseurs
- Identification de raccords de tuyaux dans des zones stériles
- Identification de raccords de tuyaux dans des zones explosives de classe 1
- Identification de big bags et de bioréacteurs
- Identification de produits à usage unique
- Semi-conducteur
- Vérification du marquage électronique
- Comptage des circuits intégrés
- Contrôle de deux codes-barres
- Commande de sécurité compacte
- Protection des petits points d'accès
- Éclairage d'un outil de production dans le secteur des semi-conducteurs
- Détection d'adhésif sur l'assemblage de PCB
- Détection du centre de plaques à l'aide du DF-G2
- Inspection approfondie des appareils électroniques mobiles
- Vérification d'erreurs pour les puces de circuits intégrés chargées dans la bande support
- Présence et orientation des puces de CI placées dans les nids
- Détection de disques durs
- Station d'assemblage multiproduits à guidage optique
- Indication de l'état grâce aux LED pendant la fabrication des semi-conducteurs
- Protection des petits points d'accès
- Success Stories